Monopaste or coextruded WPC composite wood
Monopaste or coextruded WPC composite wood
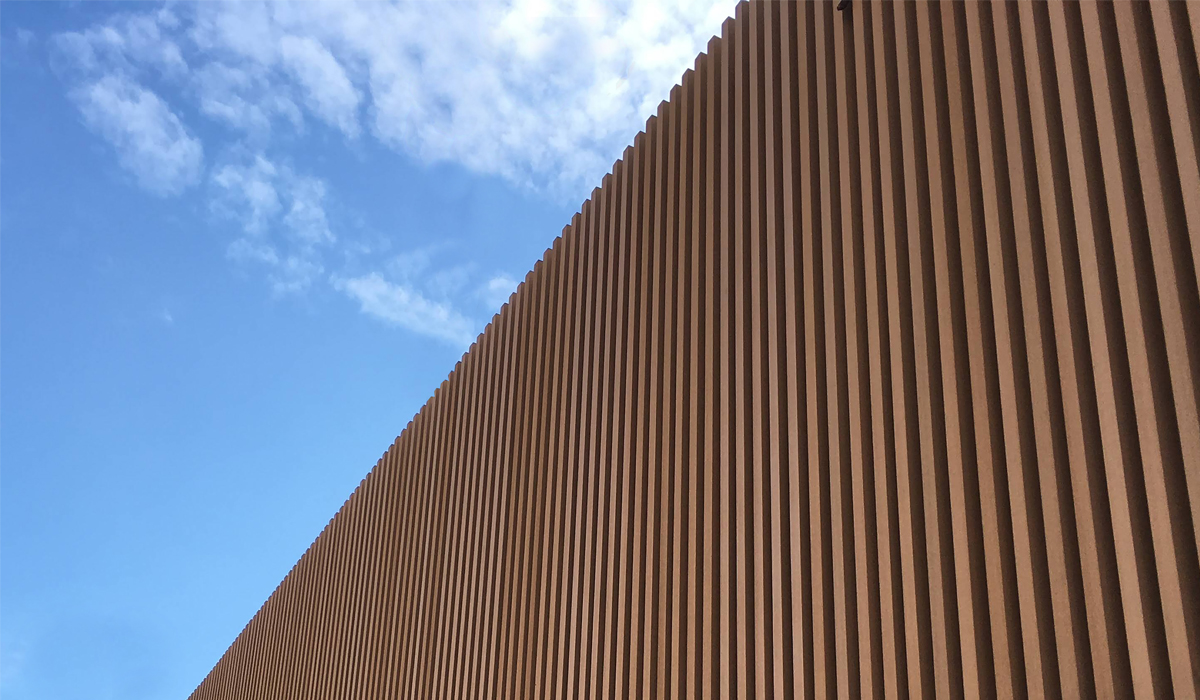
The monopaste product has very important characteristics thanks to the components that are inserted within the formulation. The 3 main components are Wood, Polymer and Additives, agglomerated in a single mixture in a homogeneous way through a single extrusion process. For all composite woods the rule is that the higher the quality of the main products, the better the durability of the product. The components must be mixed according to a precise ratio between them and extruded with an adequate pressure in order to obtain a product of high durability.
For more information on composite wood go to BLOG What is composite wood
Following the increase in market demand coming mainly from the markets of America and Europe, due to the greater and growing competitiveness between competing products and to the need to find alternative solutions to single-stick composite wood.
Some manufacturers have started research aimed at finding solutions that could lower the costs of the 3 macro-components (wood, polymer and additives). The result was to find a product that could cover the inner part of the material (the so-called "core") with a protective plastic film with a thickness ranging from a few tenths of a millimeter to a few tenths (normally from 0.05 to 0 , 6 mm.). This is in order to reduce the amount of additives inserted in the "core" (which in the case of the monopasta can cost almost 50% of the finished product) thanks to a film that should "seal" it from attacks deriving from external atmospheric agents (oxygen , humidity and UV rays).
This process takes place by applying, downstream of the main extruder matrix, a second extruder which injects, during the extrusion phase, a very liquid composite with a prevalence of polymers that covers the main extrudate (Core) already partially solidified previously. The process is very complex, the compounds and the melting temperatures between the two compounds are essential to ensure that the product does not separate over time. The profile thus produced takes the name of coextruded or second generation composite wood, precisely because it was born in the years following the first, but this does not mean that it is a positive or better evolution of the first single-stick, simply a different product is extruded.
Below we see strengths and weaknesses and what characteristics differentiate the two product categories.
Published on 12 November 2020
You may also be interested in
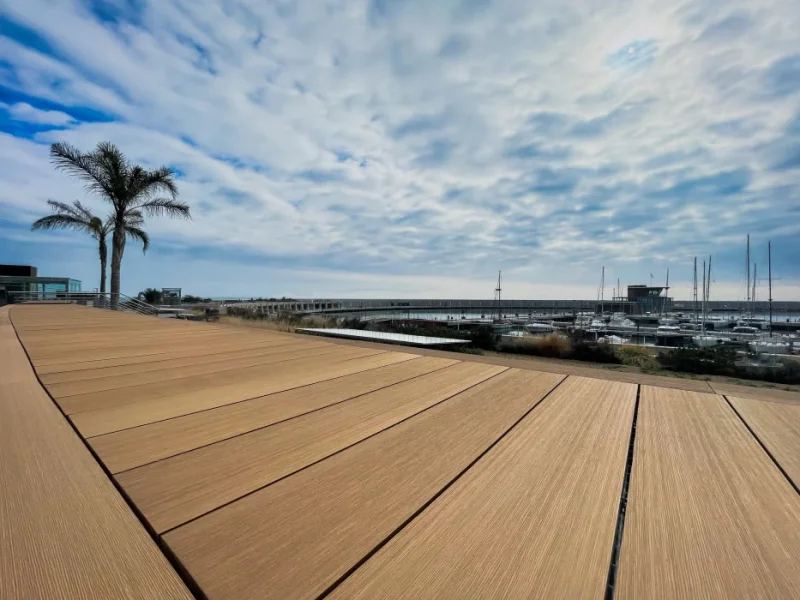
Novowood WPC Floors
Choosing the right outdoor floor is essential to combine aesthetics, functionality, and longevity. Today, WPC floor represents one of the mo… Read more
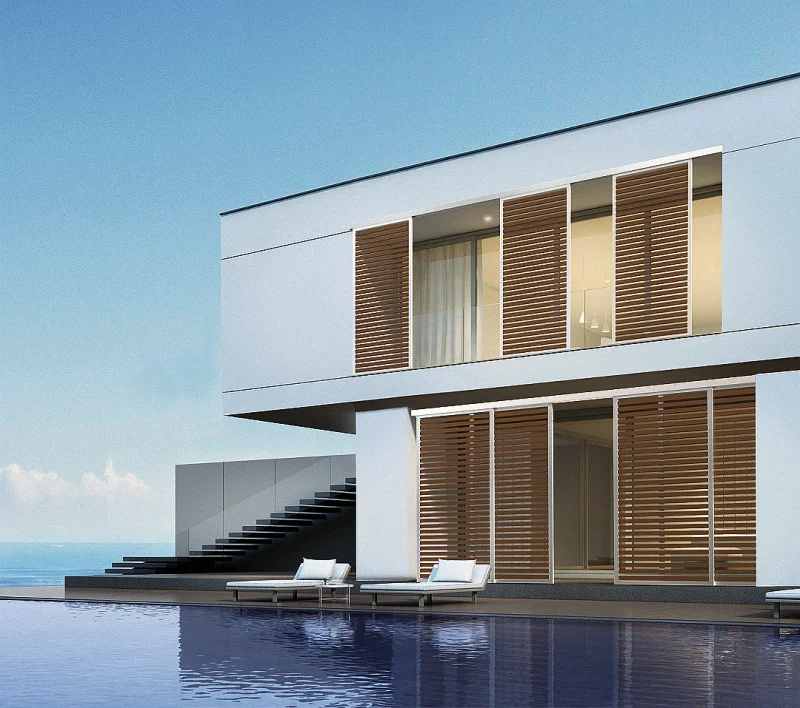
Discover the Benefits of Sliding Panels for Summer Comfort
With the arrival of summer, homes are exposed to sunlight for extended periods, significantly heating up the interiors. This leads to a substantial us… Read more
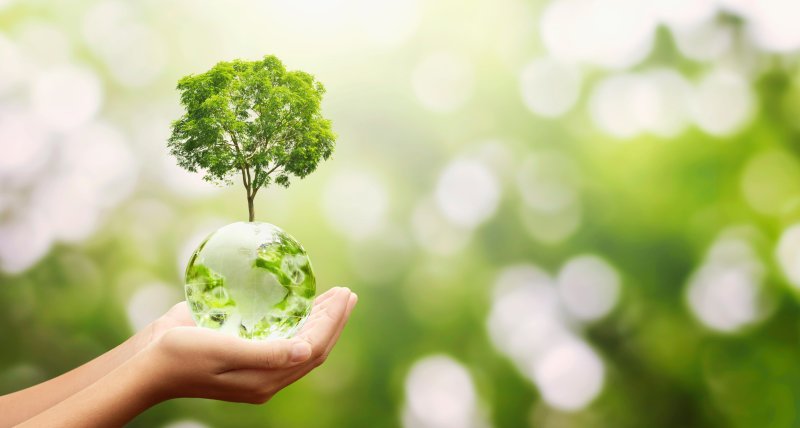
We respect the environment, we respect ourselves.
Today we are finally aware of how much our behaviour affects the environment around us: saving raw materials, CO2 emissions have become topics of co… Read more
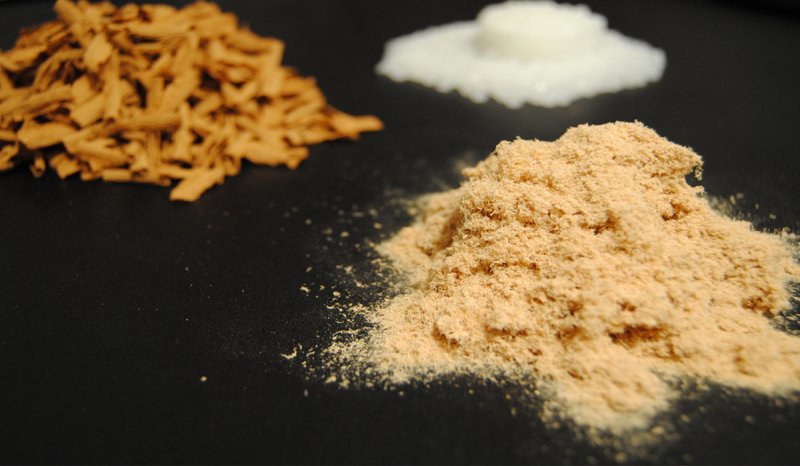
What's WPC composite wood?
Composite wood is a product that was born as an ecological substitute for outdoor wood. It is also called WPC as an acronym for Wood Plastic Composite… Read more
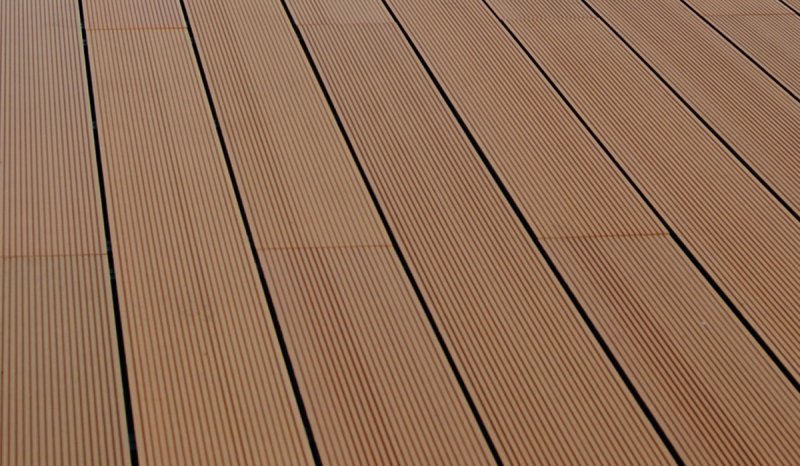
Maintenance of wpc composite wood
Composite wood was created mainly to avoid the maintenance, typical of natural wood. So there are no sanding and no painting operations, no proce… Read more
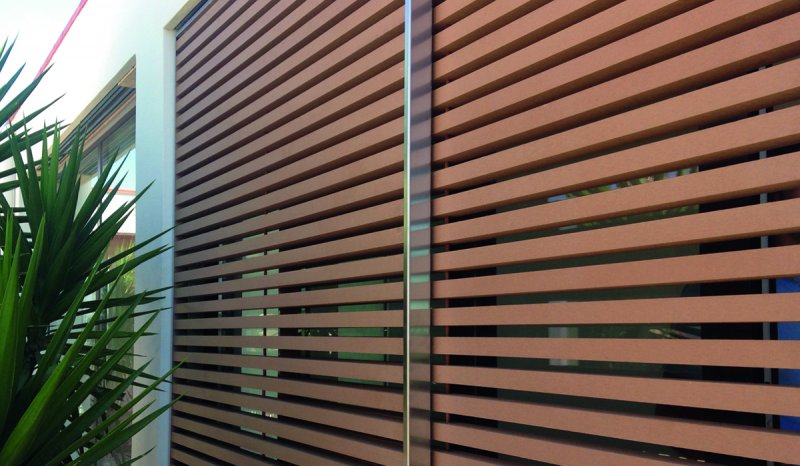
Louvers in WPC-composite wood
Try to think of a beautiful wooden sunshade. Beautiful when it is just installed but after a few months the graying begins. For some people this is th… Read more
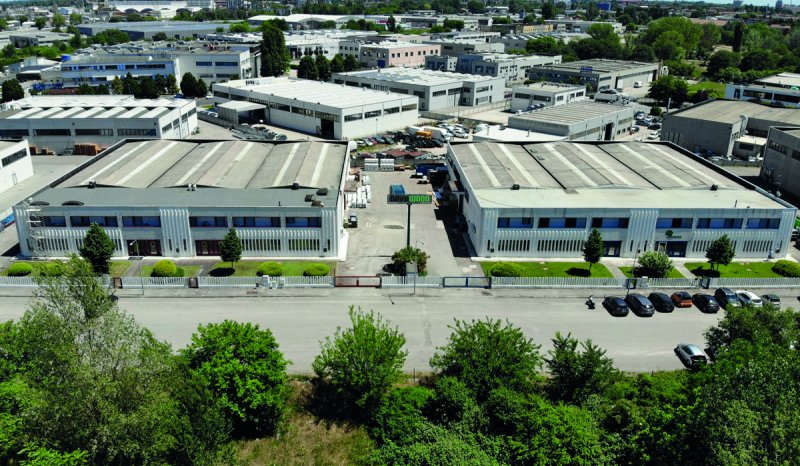
WPC composite wood Made in Italy
Made in Italy determines the origin of production of the materials. Made in Italy is a feature that is appreciated all over the world. Why: Made in I… Read more
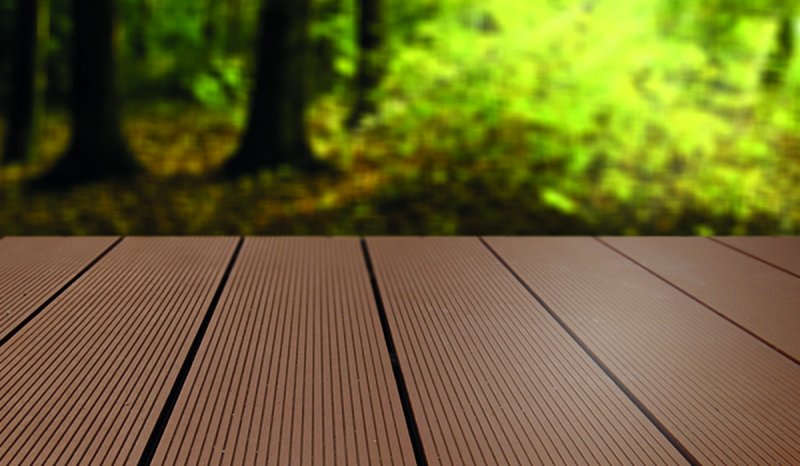
wpc composite wood prices
What is the right price for a composite? This is a question that many web users are looking for to understand why there can be prices on the market wi… Read more