Bois composite simple ou co-extrudé
Bois composite simple ou co-extrudé
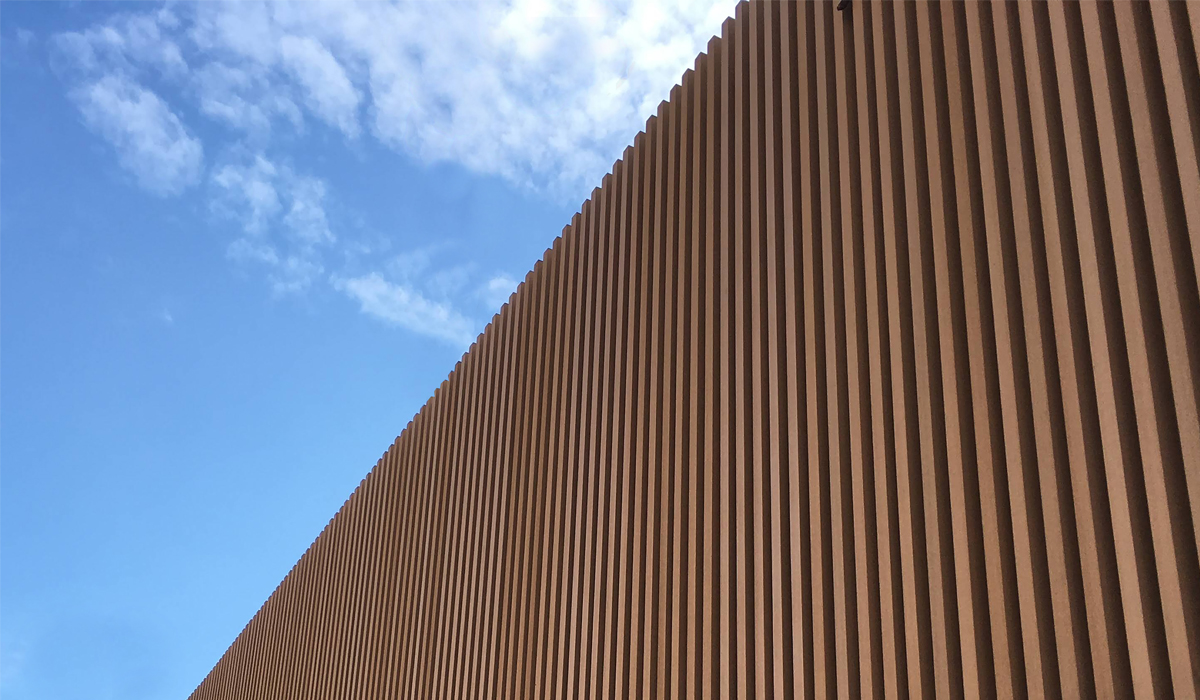
Le bois composite est né au début des années 2000 comme produit de substitution au bois. C'est pour ces raisons qu'il a été conçu comme un produit mono-pâte dont l'aspect est semblable à celui du bois : cela signifie que le produit est constitué, dans sa totalité, d'un seul matériau composite qui a été préalablement malaxé.
Le produit mono-pâte présente des caractéristiques très intéressantes, et cela est dû aux composants qui sont incorporés dans sa formulation. Les trois principaux composants sont le bois, le polymère et les additifs, qui sont agglomérés de manière homogène en une seule pâte grâce à un processus d'extrusion unique. Pour tous les bois composites, la règle veut que plus la qualité des produits principaux est élevée, plus la durabilité du produit est grande. Les composants doivent être mélangés selon un rapport précis et extrudés avec une pression adéquate afin d'obtenir un produit à haute durabilité.
Pour plus d'informations sur le bois composite, consultez la section du BLOG « Qu' est-ce que le bois composite ? »
Suite à l'augmentation de la demande provenant principalement des marchés américains et européens, en raison de la compétitivité accrue et croissante entre les produits concurrents et afin de trouver des solutions alternatives au bois composite mono-pâte, certains fabricants ont commencé à faire des recherches pour trouver le moyen de réduire les coûts des trois macro-composants (bois, polymère et additifs). Ces recherches ont mené à la création d’un produit dont la partie intérieure du matériau (le « noyau ») est recouverte d'un film plastique de protection ayant une épaisseur de quelques centièmes à quelques dixièmes de millimètre (en règle générale entre 0,05 et 0,6 mm). Ceci afin de réduire la quantité d'additifs insérés dans le noyau (qui, dans le cas d’une mono-pâte, peut coûter près de 50 % du produit fini) grâce à un film qui a la fonction de l’imperméabiliser contre les attaques des agents atmosphériques externes (oxygène, humidité et rayons UV).
Ce procédé se déroule en appliquant, en aval de la matrice de l'extrudeuse principale, une seconde extrudeuse qui injecte, pendant la phase d'extrusion, un composite très liquide, à prédominance polymère, qui recouvre le produit extrudé principal (le noyau) déjà partiellement solidifié au préalable. Le processus est très complexe : les composés et leurs températures de fusion sont cruciaux pour garantir que le produit ne se sépare pas au fil du temps. Le profilé ainsi réalisé est appelé bois composite co-extrudé ou de deuxième génération, précisément parce qu'il est né de nombreuses années après le premier, mais cela ne signifie pas qu'il s'agit d'une évolution positive ou meilleure par rapport au bois composite mono-pâte, tout simplement il s’agit d’un produit extrudé différent. Nous voyons ci-dessous les avantages et inconvénients de chaque produit, ainsi que les caractéristiques qui différencient ces deux catégories.
Les caractéristiques:
Les caractéristiques esthétiques:
Le bois composite mono-pâte est chaud au toucher, la fibre de bois à vue évoque immédiate le bois naturel. Sur le plan esthétique, il est homogène et, s'il est de haute qualité, on peut même sentir l'odeur du bois. Les propriétés esthétiques du produit mono-pâte peuvent être répliquées même dans les produits co-extrudés, grâce à la création de motifs et de nuances à la surface du film plastique. Dans ce cas, le produit est froid au toucher et brillant lorsqu'il est vu à contre-jour. Pour réduire l'effet plastique, certains fabricants pratiquent le ponçage de surface, mais cela réduit encore l'épaisseur du film et crée des pelures plastiques inesthétiques.
Découpe et façonnage sur bois composite:
Le façonnage sur le produit mono-pâte est réalisé de la même manière que sur le bois naturel, sans aucune limitation et en conservant les caractéristiques esthétiques et de performance du produit. Le résultat est compact et uniforme, même dans la zone de coupe. En revanche, un produit co-extrudé soumis à des façonnages tels que les coupes longitudinales ou le fraisage, expose le matériau interne aux agents atmosphériques en le privant de sa barrière de protection, exposant ainsi la partie la moins noble du produit, le noyau, qui n'est pas conçue pour rester en contact avec les agents atmosphériques externes. Le produit n'a pas été pensé pour être soumis à un usinage mécanique, et qui dit usinage dit création de chocs mécaniques entre le noyau et le film protecteur. Les coupes aux extrémités ou celles nécessaires pour couper la longueur de la lame créent aussi fréquemment des problèmes d'exfoliation de la barrière de protection.
Il faut également tenir compte des opérations de façonnage général sur les profilés ou des opérations de menuiserie sur les lames telles que les moulures dites « tore » et « bec de corbin ». Dans le cas du produit co-extrudé, ces possibilités ne sont pas envisageables : il n'est pas possible de l'usiner car cela exposerait le noyau à une oxydation prématurée. Dans toutes les parties où le noyau est exposé, la partie faible du produit l'est aussi et, comme mentionné ci-dessus, cela entraîne la formation d’une zone non protégée dans la structure.
Les deux produits doivent être travaillés avec des outils appropriés et de préférence avec des disques de coupe en carburé cémenté.
Risques de tâche sur le WPC
Les deux types de produits peuvent absorber des liquides en surface et créer des taches.
Les produits mono-pâte qui ont été formulés avec des additifs de qualité n'absorbent pas les taches en profondeur et ont une bonne résistance aux produits extérieurs en général. Le nettoyage est facile et si des produits spécifiques sont utilisés, presque tous les types de taches peuvent être éliminés complètement. Le produit co-extrudé, ayant un film extérieur en plastique, a une absorption encore plus faible. Mais même dans ce cas, il est nécessaire de nettoyer la tache dès que possible pour éviter les auréoles. En cas de tache difficile, le produit mono-pâte peut toujours être légèrement poncé pour enlever l'auréole, même si le liquide est absorbé plus en profondeur. La pâte étant identique, cette opération peut être réalisée sans compromettre le produit. Dans le produit co-extrudé, cette opération n'est pas possible, car le film est très fin. Si des auréoles sont présentes, il n'y a pas d'autre solution que de remplacer la lame.
VOIR BLOG NETTOYAGE DU BOIS COMPOSITE
Rayures en surface
En ce qui concerne la possibilité éventuelle de rayer ou d'érafler la surface, le mono-pâte présente des avantages considérables : le produit peut être poncé avec un papier abrasif moyen pour restaurer le produit. Quant au co-extrudé, en cas de rayures, le produit ne peut pas être restauré et doit être remplacé.
Recyclage du bois composite et économie circulaire
Le recyclage des produits est une question extrêmement importante et d'actualité. Seuls certains produits mono-pâte peuvent être régénérés. Les entreprises de fabrication qui ont mené des études de formulation et réalisent des produits recyclables dès la première extrusion peuvent être contactées en fin de vie du produit pour procéder au recyclage de ce dernier. Le procédé, proposé pour la première fois en 2005 par Novowood, a permis à plusieurs fabricants de s’approcher de cette vision et est désormais devenu un objectif environnemental très prisé. En outre, cela transporte les fabricants directement à l'intérieur de la chaîne de l'économie circulaire, qui implique à la fois les producteurs et les utilisateurs. Ce procédé permet ainsi de réduire et d'éviter l'exploitation des ressources de la planète pour la création de nouveaux matériaux. Cette régénération n'est pas possible ni avec les produits mono-pâte, qui ne sont pas conçus à l'origine pour une telle réutilisation, ni avec les produits co-extrudés, car ce sont des produits composés de 2 éléments différents, la protection extérieure en plastique et le noyau intérieur. Bien entendu, ce processus est possible exclusivement avec des produits de première génération fabriqués en Italie : les produits importés ne disposent pas dans le pays d’importation d'entreprises capables de s’occuper de la régénération du produit.
Certains commerçants de bois composite co-extrudé, afin de rendre moins évidents les difficultés liées au recyclage du matériau, font état de caractéristiques plutôt « bizarres » de leur produits, par exemple en lui attribuant un pourcentage de plastique biodégradable dans la composition. De toute évidence, aucun polymère pouvant être inséré dans le bois composite n'est biodégradable... si tel était le cas, le matériau vendu serait "biodégradable" même pendant son cycle de vie, ce qui ne serait évidemment pas à l'avantage de l'utilisateur final.
Face à ce qui précède, malgré l'évolution du marché et la croissance constante des prix des matières premières, de nombreuses entreprises ont maintenu une production stable de produits extrudés mono-pâte de première génération, tandis que beaucoup d'autres, qui ont expérimenté de nouvelles technologies liées à la co-extrusion du bois composite, sont revenues sur leurs pas au fil du temps en raison de la difficulté de produire un produit stable dans le temps et pouvant réellement avoir une garantie de durabilité sans problèmes liés au film protecteur.
En Italie, aucune entreprise de bois composite n'a jamais choisi de transformer sa production en matériaux co-extrudés.
Publié le 12 novembre 2020
Les caractéristiques esthétiques:
Le bois composite mono-pâte est chaud au toucher, la fibre de bois à vue évoque immédiate le bois naturel. Sur le plan esthétique, il est homogène et, s'il est de haute qualité, on peut même sentir l'odeur du bois. Les propriétés esthétiques du produit mono-pâte peuvent être répliquées même dans les produits co-extrudés, grâce à la création de motifs et de nuances à la surface du film plastique. Dans ce cas, le produit est froid au toucher et brillant lorsqu'il est vu à contre-jour. Pour réduire l'effet plastique, certains fabricants pratiquent le ponçage de surface, mais cela réduit encore l'épaisseur du film et crée des pelures plastiques inesthétiques.
Découpe et façonnage sur bois composite:
Le façonnage sur le produit mono-pâte est réalisé de la même manière que sur le bois naturel, sans aucune limitation et en conservant les caractéristiques esthétiques et de performance du produit. Le résultat est compact et uniforme, même dans la zone de coupe. En revanche, un produit co-extrudé soumis à des façonnages tels que les coupes longitudinales ou le fraisage, expose le matériau interne aux agents atmosphériques en le privant de sa barrière de protection, exposant ainsi la partie la moins noble du produit, le noyau, qui n'est pas conçue pour rester en contact avec les agents atmosphériques externes. Le produit n'a pas été pensé pour être soumis à un usinage mécanique, et qui dit usinage dit création de chocs mécaniques entre le noyau et le film protecteur. Les coupes aux extrémités ou celles nécessaires pour couper la longueur de la lame créent aussi fréquemment des problèmes d'exfoliation de la barrière de protection.
Il faut également tenir compte des opérations de façonnage général sur les profilés ou des opérations de menuiserie sur les lames telles que les moulures dites « tore » et « bec de corbin ». Dans le cas du produit co-extrudé, ces possibilités ne sont pas envisageables : il n'est pas possible de l'usiner car cela exposerait le noyau à une oxydation prématurée. Dans toutes les parties où le noyau est exposé, la partie faible du produit l'est aussi et, comme mentionné ci-dessus, cela entraîne la formation d’une zone non protégée dans la structure.
Les deux produits doivent être travaillés avec des outils appropriés et de préférence avec des disques de coupe en carburé cémenté.
Risques de tâche sur le WPC
Les deux types de produits peuvent absorber des liquides en surface et créer des taches.
Les produits mono-pâte qui ont été formulés avec des additifs de qualité n'absorbent pas les taches en profondeur et ont une bonne résistance aux produits extérieurs en général. Le nettoyage est facile et si des produits spécifiques sont utilisés, presque tous les types de taches peuvent être éliminés complètement. Le produit co-extrudé, ayant un film extérieur en plastique, a une absorption encore plus faible. Mais même dans ce cas, il est nécessaire de nettoyer la tache dès que possible pour éviter les auréoles. En cas de tache difficile, le produit mono-pâte peut toujours être légèrement poncé pour enlever l'auréole, même si le liquide est absorbé plus en profondeur. La pâte étant identique, cette opération peut être réalisée sans compromettre le produit. Dans le produit co-extrudé, cette opération n'est pas possible, car le film est très fin. Si des auréoles sont présentes, il n'y a pas d'autre solution que de remplacer la lame.
VOIR BLOG NETTOYAGE DU BOIS COMPOSITE
Rayures en surface
En ce qui concerne la possibilité éventuelle de rayer ou d'érafler la surface, le mono-pâte présente des avantages considérables : le produit peut être poncé avec un papier abrasif moyen pour restaurer le produit. Quant au co-extrudé, en cas de rayures, le produit ne peut pas être restauré et doit être remplacé.
Recyclage du bois composite et économie circulaire
Le recyclage des produits est une question extrêmement importante et d'actualité. Seuls certains produits mono-pâte peuvent être régénérés. Les entreprises de fabrication qui ont mené des études de formulation et réalisent des produits recyclables dès la première extrusion peuvent être contactées en fin de vie du produit pour procéder au recyclage de ce dernier. Le procédé, proposé pour la première fois en 2005 par Novowood, a permis à plusieurs fabricants de s’approcher de cette vision et est désormais devenu un objectif environnemental très prisé. En outre, cela transporte les fabricants directement à l'intérieur de la chaîne de l'économie circulaire, qui implique à la fois les producteurs et les utilisateurs. Ce procédé permet ainsi de réduire et d'éviter l'exploitation des ressources de la planète pour la création de nouveaux matériaux. Cette régénération n'est pas possible ni avec les produits mono-pâte, qui ne sont pas conçus à l'origine pour une telle réutilisation, ni avec les produits co-extrudés, car ce sont des produits composés de 2 éléments différents, la protection extérieure en plastique et le noyau intérieur. Bien entendu, ce processus est possible exclusivement avec des produits de première génération fabriqués en Italie : les produits importés ne disposent pas dans le pays d’importation d'entreprises capables de s’occuper de la régénération du produit.
Certains commerçants de bois composite co-extrudé, afin de rendre moins évidents les difficultés liées au recyclage du matériau, font état de caractéristiques plutôt « bizarres » de leur produits, par exemple en lui attribuant un pourcentage de plastique biodégradable dans la composition. De toute évidence, aucun polymère pouvant être inséré dans le bois composite n'est biodégradable... si tel était le cas, le matériau vendu serait "biodégradable" même pendant son cycle de vie, ce qui ne serait évidemment pas à l'avantage de l'utilisateur final.
Face à ce qui précède, malgré l'évolution du marché et la croissance constante des prix des matières premières, de nombreuses entreprises ont maintenu une production stable de produits extrudés mono-pâte de première génération, tandis que beaucoup d'autres, qui ont expérimenté de nouvelles technologies liées à la co-extrusion du bois composite, sont revenues sur leurs pas au fil du temps en raison de la difficulté de produire un produit stable dans le temps et pouvant réellement avoir une garantie de durabilité sans problèmes liés au film protecteur.
En Italie, aucune entreprise de bois composite n'a jamais choisi de transformer sa production en matériaux co-extrudés.
Ça pourrait vous intéresser
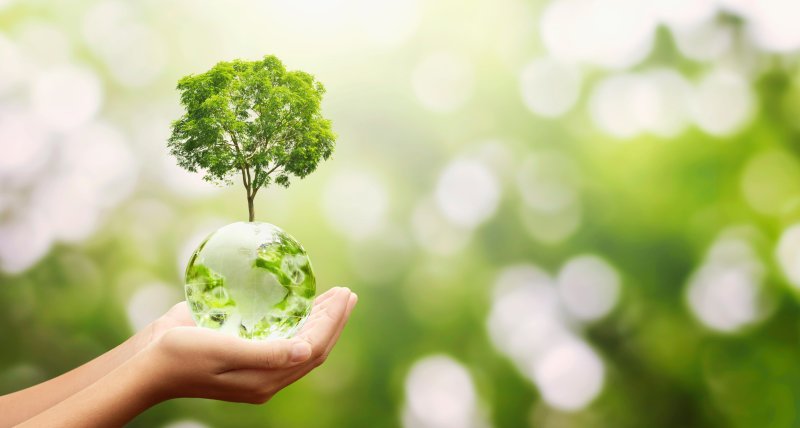
Nous respectons l’environnement et nous-mêmes
Aujourd'hui, nous sommes enfin conscients de l'influence de notre comportement sur l'environnement qui nous entoure : l'économi… Tout lire
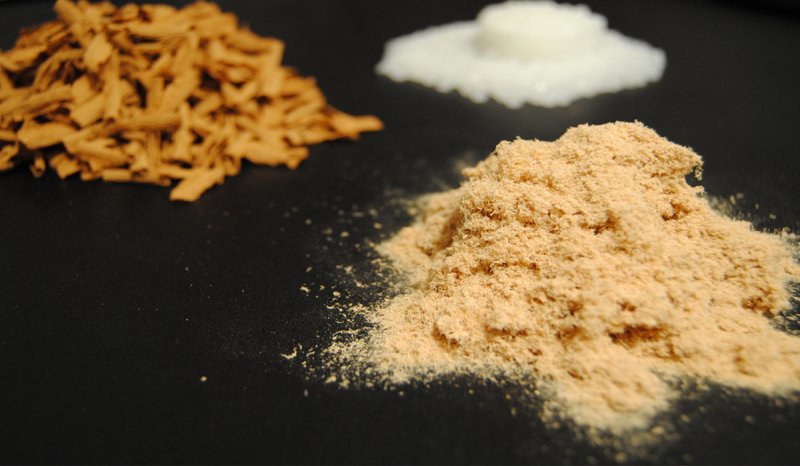
Qu'est-ce que le bois composite?
Le bois composite est un produit qui a été créé en tant que substitut écologique du bois pour les espaces en ext&ea… Tout lire
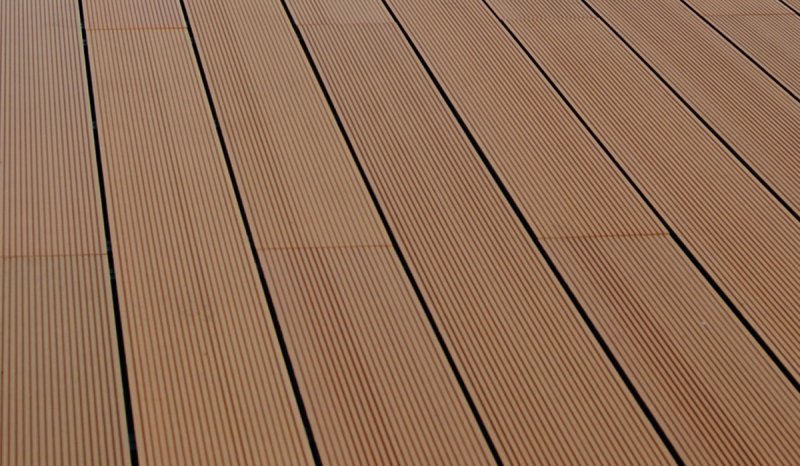
Entretien du bois composite
Le bois composite a été créé principalement pour éviter l'entretien qui doit être accordé au bois … Tout lire
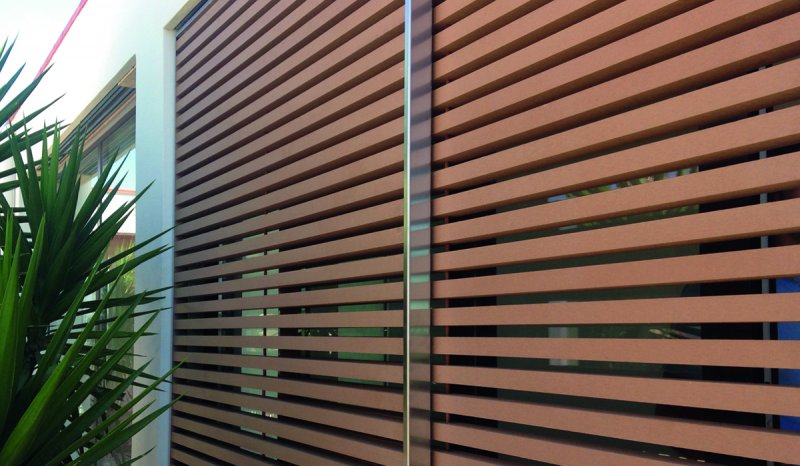
Brise-soleil en bois composite
Imaginez un beau brise-soleil en bois. Ah ça pour être beau, c’est beau ! Mais voilà qu’après quelques mois, vo… Tout lire
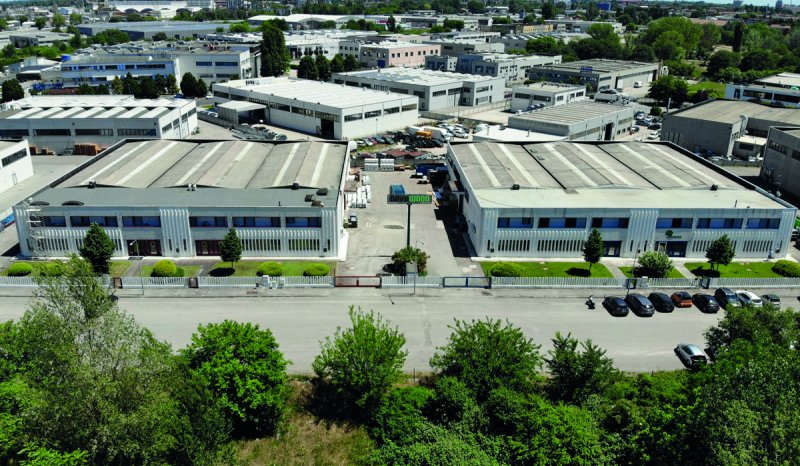
Bois composite 100 % italien
Le Made in Italy est une assurance de l'origine de production des matériaux. Le Made in Italy est une caractéristique appréc… Tout lire
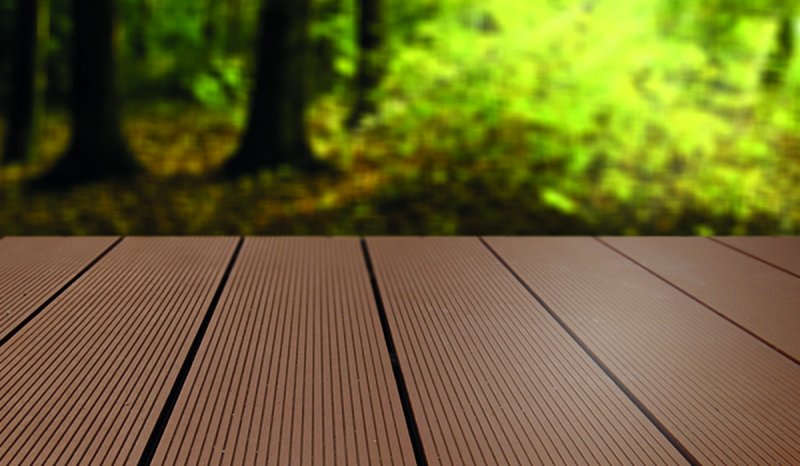
Prix du bois composite
Quel est le juste prix pour un bois composite ? C'est une question que de nombreux internautes se posent. Nous expliquons aujourd’hui ce qui… Tout lire