Legno composito monopasta o coestruso
Caratteristiche e differenze
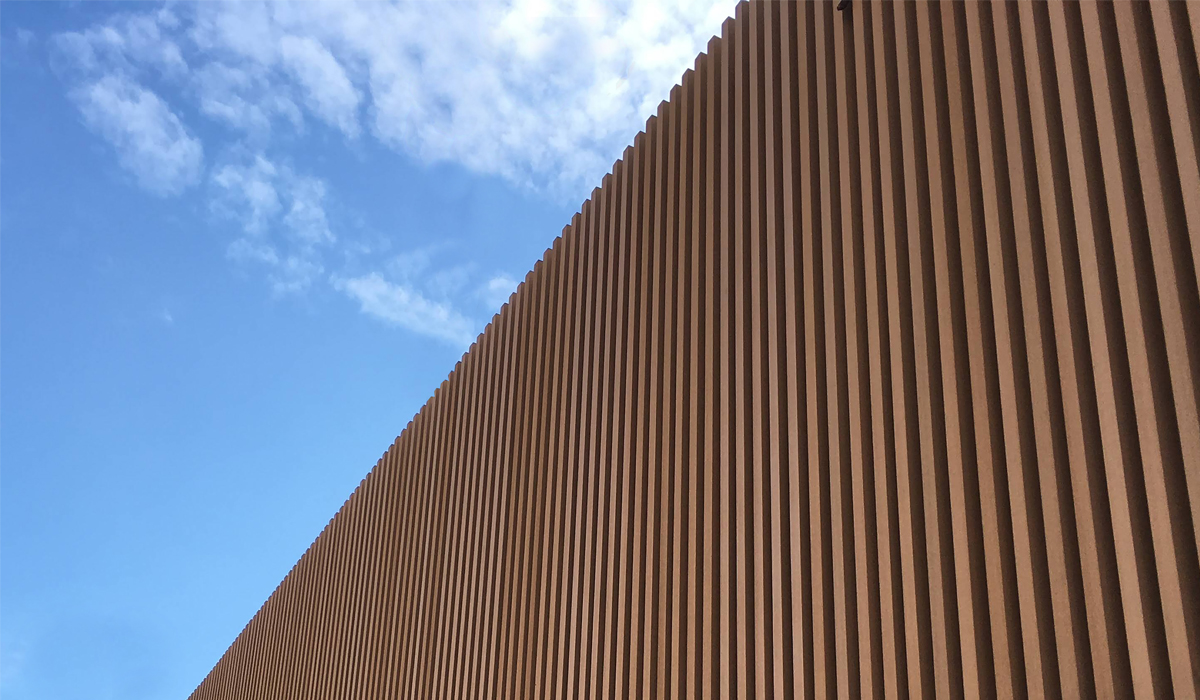
Il legno composito nasce agli inizi del 2000 come prodotto sostitutivo del legno. Per tali motivi è stato concepito in monopasta molto simile all’aspetto estetico del legno: questo significa che il prodotto è costituito, per la sua totalità, da un unico materiale composito precedentemente miscelato.
Il prodotto monopasta ha caratteristiche molto importanti e questo grazie alle componenti che vengono inserite all’interno della formulazione. Le 3 componentistiche principali sono Legno, Polimero e Additivi, agglomerati in un unico impasto in maniera omogenea attraverso un processo unico di estrusione. Per tutti i legni compositi vale la regola che maggiore è qualità dei prodotti principali e migliore sarà la durabilità del prodotto. I componenti dovranno essere miscelati secondo un rapporto ben preciso tra essi ed estrusi con una pressione adeguata in maniera tale da ottenere un prodotto di durabilità elevata. Per maggiori informazioni relative al legno composito leggi il nostro articolo: Cos’è il legno composito
A seguito dell’incremento della domanda di mercato proveniente principalmente dai mercati dell’America ed Europa, a causa della maggiore e crescente competitività tra prodotti concorrenti e per trovare soluzioni di alterative al legno composito monopasta, alcuni produttori hanno iniziato delle ricerche volte a trovare soluzioni che potessero abbassare i costi delle 3 macro-componenti (legno, polimero e additivi). Il risultato è stato di trovare un prodotto che potesse rivestire la parte interna del materiale (il cosiddetto “core”) con una pellicola protettiva di plastica di spessore che varia da qualche decimo centesimo di millimetro a qualche decimo (normalmente da 0,05 a 0,6 mm.). Questo al fine di diminuire la quantità degli additivi inseriti nel “core” (che nel caso del monopasta possono arrivare a costare quasi il 50% del prodotto finito) grazie ad una pellicola che dovrebbe “sigillarlo” dagli attacchi derivanti da agenti atmosferici esterni (ossigeno, umidità e raggi UV).
Questo processo avviene applicando, a valle della matrice dell’estrusore principale, un secondo estrusore che inietta, in fase di estrusione, un composito molto liquido a prevalenza polimerica che va a ricoprire l’estruso principale (Core) già parzialmente solidificato in precedenza. Il processo è molto complesso, i composti e le temperature di fusione tra i due composti sono fondamentali per far sì che il prodotto non si separi nel tempo. Il profilo così prodotto prende il nome di legno composito coestruso o di seconda generazione proprio perché nasce negli anni successivamente alla prima, ma ciò non significa che sia un’evoluzione positiva o migliore della prima monopasta, semplicemente viene estruso un prodotto differente. Di seguito vediamo pregi e difetti e quali caratteristiche differenziano le due categorie di prodotto.
Le caratteristiche:
Le caratteristiche estetiche:
Il legno composito monopasta risulta essere caldo al tatto, la fibra di legno esposta dona la caratteristica di associazione immediata al legno naturale. Esteticamente risulta omogeneo e se di alta qualità si può odorare il profumo del legno. Le proprietà estetiche del prodotto monopasta si cercano di eguagliare anche nei prodotti coestrusi con la creazione disegni e sfumature sulla superficie della pellicola plastica. Il prodotto in questo caso risulta freddo al tatto e lucido se guardato in controluce. Per ridurre l’effetto plastico alcuni produttori pratica una levigatura superficiale ma che riduce ulteriormente lo spessore della pellicola e crea peletti plastici inestetici.
I tagli e le lavorazioni sul legno composito:
Le lavorazioni sul prodotto monoimpasto vengono eseguite come sul legno naturale senza alcuna limitazione e mantenendo inalterate le caratteristiche estetiche e prestazionali del prodotto. Il risultato si mostra compatto e uniforme anche nella zona di taglio. Un prodotto coestruso sottoposto a lavorazioni come tagli longitudinali o fresature espone invece il materiale interno agli agenti atmosferici privandoli del suo scudo protettivo, viene quindi esposta la parte meno nobile del prodotto, il Core, che non è stata creata per mantenersi a contatto con gli agenti atmosferici esterni. Il prodotto non è concepito per essere sottoposto a lavorazioni meccaniche e praticare lavorazioni significa creare shock meccanici tra core e film protettivo. Anche i tagli di intestatura o quelli necessari per tagliare in lunghezza la doga creano frequentemente problemi di esfoliazione della scudo protettivo.
Una riflessione va fatta anche relativamente alle lavorazioni generiche sui profili o operazioni di falegnameria sulle doghe come “tori” e “mezzitori”. Nel caso del coestruso non sono possibili: non si ha la possibilità di lavorarlo in quanto si esporrebbe il “core” ad un’ossidazione precoce. Tutte le parti in cui il core è a vista, viene esposta la parte debole del prodotto e, come suddetto, viene creata una zona non protetta della struttura. Entrambi i prodotti devono essere lavorati tramite strumenti adeguati e preferibilmente con denti al Vidia.
Macchiabilità del WPC
Entrambi i prodotti possono assorbire liquidi presenti sulla superficie e creare macchie. I prodotti monopasta correttamente additivati non assorbono le macchie in profondità e hanno un buona resistenza ai prodotti esterni. La pulizia risulta agevole e se utilizzati prodotti specifici si può rimuovere completamente quasi ogni tipo di macchia. Il coestruso, avendo la pellicola esterna plastica, ha un assorbimento più ridotto. Anche in questo caso è necessario pulire la macchia appena possibile per evitare aloni. Se presente una macchia difficile, per il prodotto monopasta è comunque sempre possibile carteggiare leggermente per eliminare l’alone anche se assorbita più in profondità. Essendo di tutta pasta identica, è possibile effettuare questa operazione senza compromettere il prodotto. Nel prodotto coestruso tale operazione non è possibile, essendo la pellicola moto sottile. Se presenti aloni non vi è altra soluzione che sostituire la tavola.
Scalfitture della superficie
In merito alla eventuale possibilità di graffiare o scalfire la superficie il monopasta ha notevoli vantaggi: il prodotto può essere levigato o può essere utilizzata della cartavetrata media al fine di ripristinare il prodotto. Per quanto riguarda il coestruso, in caso di scalfitture il prodotto non può essere ripristinato e deve essere sostituito.
Riciclabilità del legno composito e Circular Economy
Un tema estremamente importante e di attualità è la rigenerabilità del prodotto. Solo alcuni prodotti monopasta possono essere rigenerati. Le aziende produttrici che hanno effettuato studi sulla formulazione e che permettano già dalla prima estrusione la possibilità di recuperare il prodotto, a fine vita possono essere contattate per permettere la riciclabilità del prodotto usato. Il processo, la cui prima azienda a proporlo già dal 2005 è stata Novowood, ha permesso ad alcuni produttori di potersi adeguare a tale vision e oggi è divenuto uno traguardo ambientale molto ambito. Il processo permette di entrare a far parte della cosiddetta catena della Circular Economy, dove vengono coinvolti sia produttori che utilizzatori. Questo processo permette quindi di ridurre ed evitare lo sfruttamento di risorse del pianeta per la creazione di nuovo materiale.
Tale rigenerazione non è possibile con prodotti monoimpasto che non sono studiati all’origine per tale riuso e non è possibile con il coestruso essendo questo un prodotto composto da 2 elementi differenti, lo scudo esterno in plastica e il core interno. Naturalmente questo processo è possibile solamente con prodotti di prima generazione e che siano prodotti Made in Italy: prodotti importati non hanno sul territorio nazionale aziende che possano riprendersi il materiale e che quindi possano permettere la rigenerazione del prodotto.
Alcuni commercianti di legno composito coestruso, proprio al fine di rendere meno evidenti i problemi di riciclabilità del prodotto, riportando estroverse caratteristiche di coestruso con plastica Biodecomponibile. Evidentemente non esiste polimero inseribile nel legno composito che sia biodecomponibile… se così fosse, il materiale venduto sarebbe “biodecomponibile” anche durante il suo ciclo di vita, cosa evidentemente non di vantaggio per l’utente finale.
A fronte di quanto sopra esposto, nonostante le evoluzioni del mercato e della crescita costante dei prezzi delle materie prime, molte aziende hanno mantenuto stabile la produzione di prodotti estrusi monopasta di prima generazione, mentre molte altre, che hanno sperimentato nuove tecnologie legate alla coestrusione del legno composito, nel tempo sono ritornate sui propri passi a causa della difficoltà di produrre un prodotto stabile nel tempo e che possa effettivamente avere una garanzia di durabilità senza che si presentino problematiche legate al film protettivo.
In Italia, nessuna azienda produttrice di legno composito ha mai optato per trasformare la propria produzione per ottenere materiali coestrusi.
Pubblicato il 12 novembre 2020
Le caratteristiche estetiche:
Il legno composito monopasta risulta essere caldo al tatto, la fibra di legno esposta dona la caratteristica di associazione immediata al legno naturale. Esteticamente risulta omogeneo e se di alta qualità si può odorare il profumo del legno. Le proprietà estetiche del prodotto monopasta si cercano di eguagliare anche nei prodotti coestrusi con la creazione disegni e sfumature sulla superficie della pellicola plastica. Il prodotto in questo caso risulta freddo al tatto e lucido se guardato in controluce. Per ridurre l’effetto plastico alcuni produttori pratica una levigatura superficiale ma che riduce ulteriormente lo spessore della pellicola e crea peletti plastici inestetici.
I tagli e le lavorazioni sul legno composito:
Le lavorazioni sul prodotto monoimpasto vengono eseguite come sul legno naturale senza alcuna limitazione e mantenendo inalterate le caratteristiche estetiche e prestazionali del prodotto. Il risultato si mostra compatto e uniforme anche nella zona di taglio. Un prodotto coestruso sottoposto a lavorazioni come tagli longitudinali o fresature espone invece il materiale interno agli agenti atmosferici privandoli del suo scudo protettivo, viene quindi esposta la parte meno nobile del prodotto, il Core, che non è stata creata per mantenersi a contatto con gli agenti atmosferici esterni. Il prodotto non è concepito per essere sottoposto a lavorazioni meccaniche e praticare lavorazioni significa creare shock meccanici tra core e film protettivo. Anche i tagli di intestatura o quelli necessari per tagliare in lunghezza la doga creano frequentemente problemi di esfoliazione della scudo protettivo.
Una riflessione va fatta anche relativamente alle lavorazioni generiche sui profili o operazioni di falegnameria sulle doghe come “tori” e “mezzitori”. Nel caso del coestruso non sono possibili: non si ha la possibilità di lavorarlo in quanto si esporrebbe il “core” ad un’ossidazione precoce. Tutte le parti in cui il core è a vista, viene esposta la parte debole del prodotto e, come suddetto, viene creata una zona non protetta della struttura. Entrambi i prodotti devono essere lavorati tramite strumenti adeguati e preferibilmente con denti al Vidia.
Macchiabilità del WPC
Entrambi i prodotti possono assorbire liquidi presenti sulla superficie e creare macchie. I prodotti monopasta correttamente additivati non assorbono le macchie in profondità e hanno un buona resistenza ai prodotti esterni. La pulizia risulta agevole e se utilizzati prodotti specifici si può rimuovere completamente quasi ogni tipo di macchia. Il coestruso, avendo la pellicola esterna plastica, ha un assorbimento più ridotto. Anche in questo caso è necessario pulire la macchia appena possibile per evitare aloni. Se presente una macchia difficile, per il prodotto monopasta è comunque sempre possibile carteggiare leggermente per eliminare l’alone anche se assorbita più in profondità. Essendo di tutta pasta identica, è possibile effettuare questa operazione senza compromettere il prodotto. Nel prodotto coestruso tale operazione non è possibile, essendo la pellicola moto sottile. Se presenti aloni non vi è altra soluzione che sostituire la tavola.
Scalfitture della superficie
In merito alla eventuale possibilità di graffiare o scalfire la superficie il monopasta ha notevoli vantaggi: il prodotto può essere levigato o può essere utilizzata della cartavetrata media al fine di ripristinare il prodotto. Per quanto riguarda il coestruso, in caso di scalfitture il prodotto non può essere ripristinato e deve essere sostituito.
Riciclabilità del legno composito e Circular Economy
Un tema estremamente importante e di attualità è la rigenerabilità del prodotto. Solo alcuni prodotti monopasta possono essere rigenerati. Le aziende produttrici che hanno effettuato studi sulla formulazione e che permettano già dalla prima estrusione la possibilità di recuperare il prodotto, a fine vita possono essere contattate per permettere la riciclabilità del prodotto usato. Il processo, la cui prima azienda a proporlo già dal 2005 è stata Novowood, ha permesso ad alcuni produttori di potersi adeguare a tale vision e oggi è divenuto uno traguardo ambientale molto ambito. Il processo permette di entrare a far parte della cosiddetta catena della Circular Economy, dove vengono coinvolti sia produttori che utilizzatori. Questo processo permette quindi di ridurre ed evitare lo sfruttamento di risorse del pianeta per la creazione di nuovo materiale.
Tale rigenerazione non è possibile con prodotti monoimpasto che non sono studiati all’origine per tale riuso e non è possibile con il coestruso essendo questo un prodotto composto da 2 elementi differenti, lo scudo esterno in plastica e il core interno. Naturalmente questo processo è possibile solamente con prodotti di prima generazione e che siano prodotti Made in Italy: prodotti importati non hanno sul territorio nazionale aziende che possano riprendersi il materiale e che quindi possano permettere la rigenerazione del prodotto.
Alcuni commercianti di legno composito coestruso, proprio al fine di rendere meno evidenti i problemi di riciclabilità del prodotto, riportando estroverse caratteristiche di coestruso con plastica Biodecomponibile. Evidentemente non esiste polimero inseribile nel legno composito che sia biodecomponibile… se così fosse, il materiale venduto sarebbe “biodecomponibile” anche durante il suo ciclo di vita, cosa evidentemente non di vantaggio per l’utente finale.
A fronte di quanto sopra esposto, nonostante le evoluzioni del mercato e della crescita costante dei prezzi delle materie prime, molte aziende hanno mantenuto stabile la produzione di prodotti estrusi monopasta di prima generazione, mentre molte altre, che hanno sperimentato nuove tecnologie legate alla coestrusione del legno composito, nel tempo sono ritornate sui propri passi a causa della difficoltà di produrre un prodotto stabile nel tempo e che possa effettivamente avere una garanzia di durabilità senza che si presentino problematiche legate al film protettivo.
In Italia, nessuna azienda produttrice di legno composito ha mai optato per trasformare la propria produzione per ottenere materiali coestrusi.
Potrebbero interessarti anche
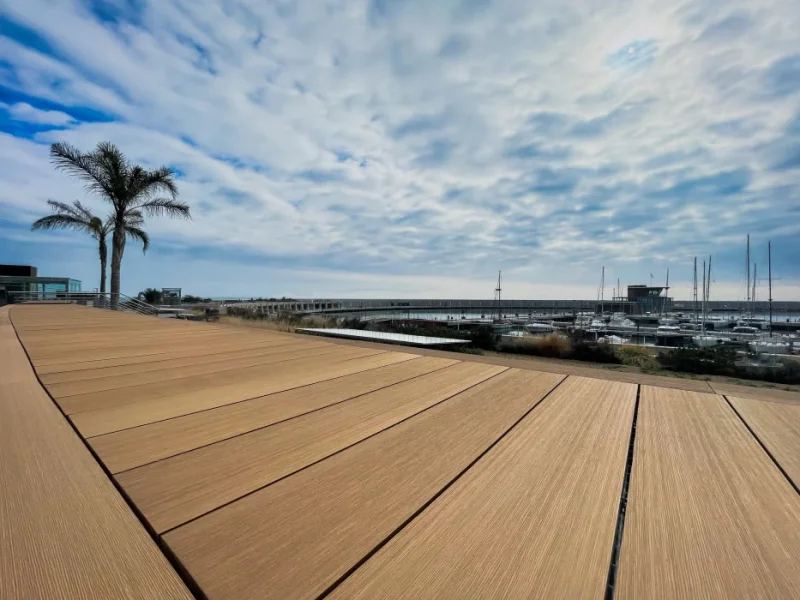
Pavimenti in WPC Novowood
Scegliere il giusto pavimento per esterni è essenziale per unire estetica, funzionalità e longevità. I pavimenti in WPC rappresen… Leggi tutto
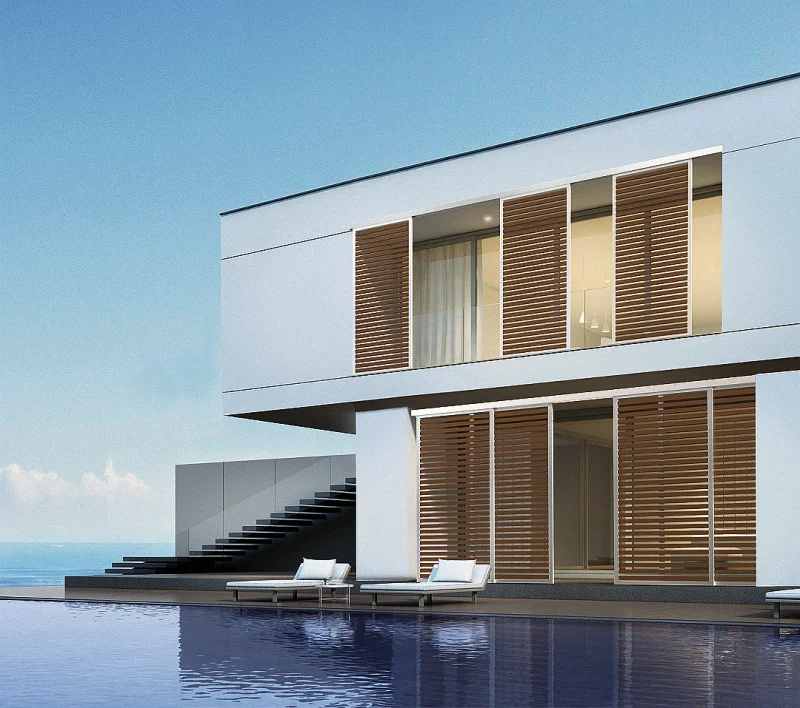
Scopri i vantaggi dei pannelli scorrevoli per il comfort estivo
Con l’arrivo dell’estate, le abitazioni sono esposte ai raggi solari per periodi prolungati surriscaldando notevolmente gli ambienti, ques… Leggi tutto
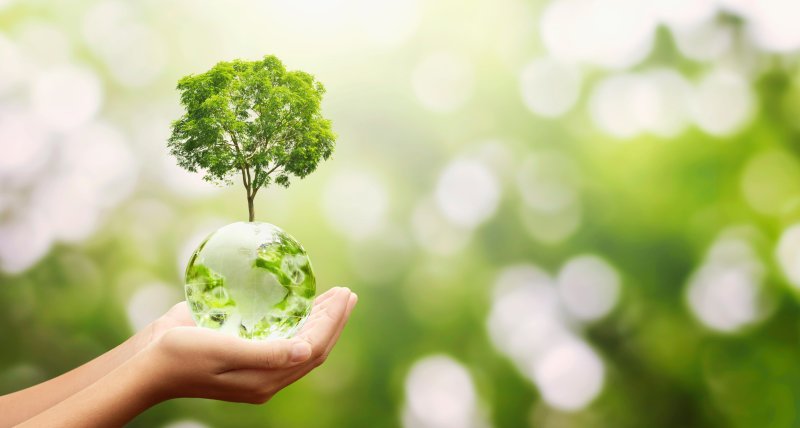
Rispettiamo l'ambiente, rispettiamo noi stessi.
Oggi siamo finalmente consapevoli di quanto i nostri comportamenti influiscano sull’ambiente che ci circonda: il risparmio di materie prime, le … Leggi tutto
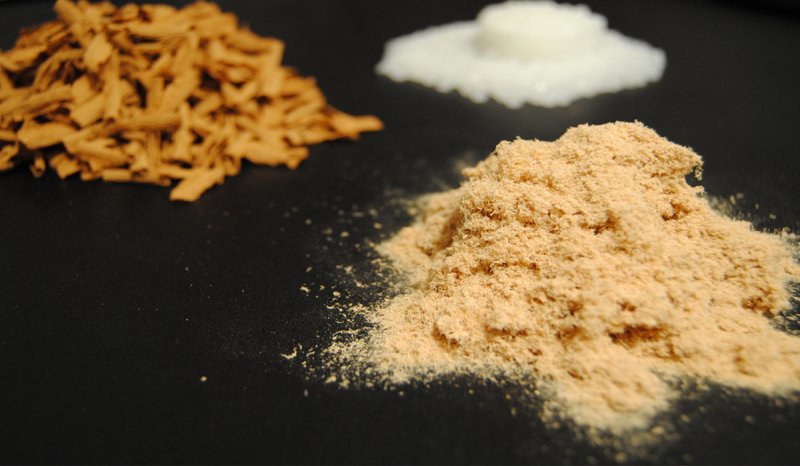
Che cos'è il legno composito?
Il Legno composito è un prodotto che nasce come sostitutivo ecologico del legno da esterno. Viene anche chiamato WPC come acronimo di Wood Plas… Leggi tutto
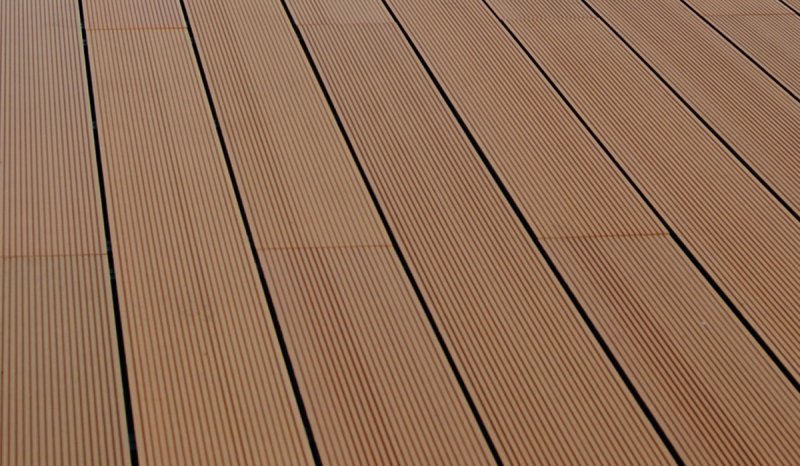
La manutenzione del legno composito
Il legno composito nasce principalmente per evitare la manutenzione tipica del legno naturale. Quindi vengono meno le operazioni di carteggiatura (o l… Leggi tutto
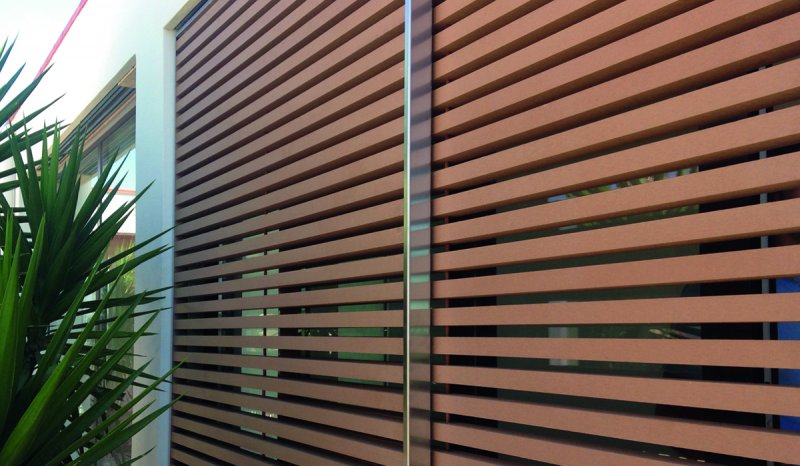
Frangisole in legno composito
Provate a pensare un bellissimo frangisole in legno. Bellissimo quando viene posato ma dopo qualche mese inizia l’ingrigimento. Per alcuni quest… Leggi tutto
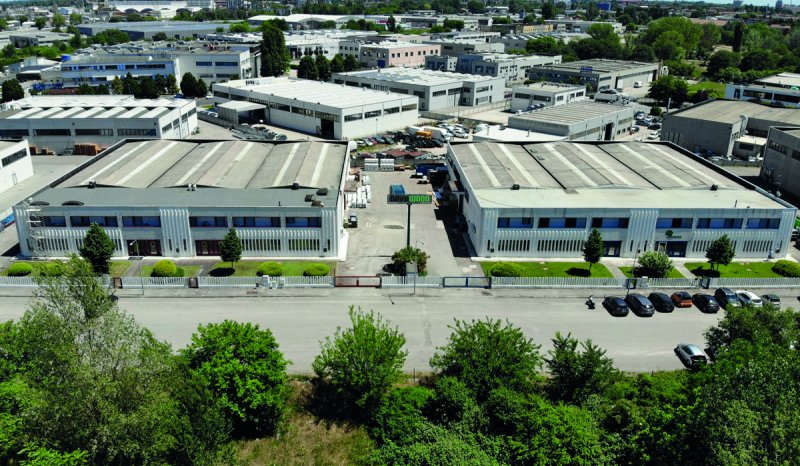
Legno composito Made In Italy
Il Made in Italy determina l’origine di produzione dei materiali. Il Made in Italy è una caratteristica che viene apprezzata in tutto il… Leggi tutto
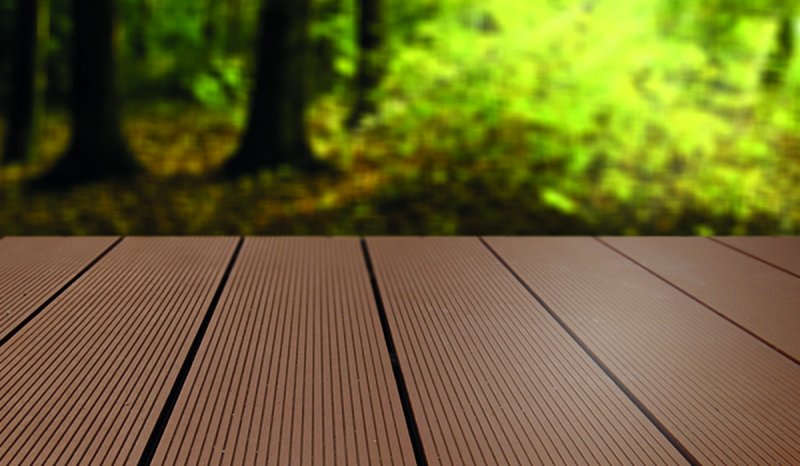
Prezzo del Legno Composito
Qual è il prezzo giusto per un composito? Questa è una domanda che si tantissimi utenti del web ricercano per comprendere perché … Leggi tutto